Services
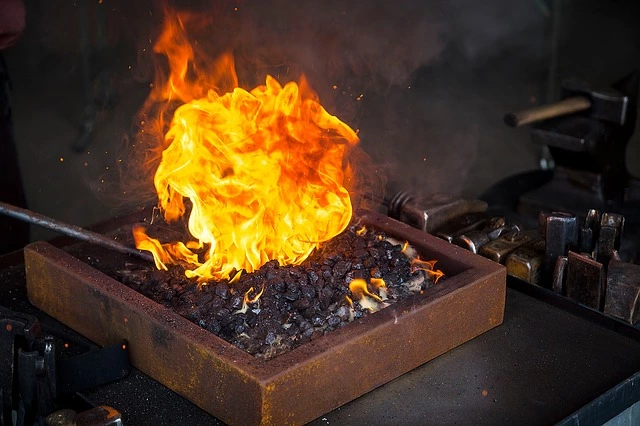
- We Are The Experts In Refractories And Can Do Value Addition For Our Patrons By Providing Complete Engineering And Design Solutions Across Various Industries And Processes.
- Refractory Lining Design & Detailed Engineering.
- Refractory Materials Selections With Detailed Specifications And Properties.
- Heat Flow Calculations.
- Refractory Anchor Design And Anchor Selection.
- Refractory Installation Standard Operating Procedures, And Quality Plan Documents.
- Heat-Up & Dry Out Schedule & Procedures.
- Preparation Of Material Requisition, TBA and Purchase Requisitions.
- We Can Also Manufacture a Wide Range Of PCPF Shapes As Per Customer Requirements And Drawings.
- This Includes Making Moulds, Castings, And Curing.
- Existing Furnace Thermography And Heat Loss Analysis
- AMC
- Onsite Lining Inspection & Assessment Of Serviceability
- Complete Refurbishment Including Fabrication
- Warranty For New Work Done
- Design And Engineering Support For Revamp / Up Gradation In Future
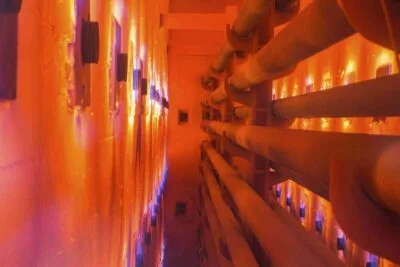
- We Are The Experts In Refractories And Can Do Value Addition For Our Patrons By Providing Complete Engineering And Design Solutions Across Various Industries And Processes.
- Refractory Lining Design & Detailed Engineering.
- Refractory Materials Selections With Detailed Specifications And Properties.
- Heat Flow Calculations.
- Refractory Anchor Design And Anchor Selection.
- Refractory Installation Standard Operating Procedures, And Quality Plan Documents.
- Heat-Up & Dry Out Schedule & Procedures.
- Preparation Of Material Requisition, TBA and Purchase Requisitions.
- We Can Also Manufacture a Wide Range Of PCPF Shapes As Per Customer Requirements And Drawings.
- This Includes Making Moulds, Castings, And Curing.
- Existing Furnace Thermography And Heat Loss Analysis
- AMC
- Onsite Lining Inspection & Assessment Of Serviceability
- Complete Refurbishment Including Fabrication
- Warranty For New Work Done
- Design And Engineering Support For Revamp / Up Gradation In Future
Our Services
Refractory Design
To minimize heat loss from the furnace, we design top-quality refractory to contain the heat generated by burning fuel.
Refractory Material Selection And Engineering
Our skilled team of engineers understands the need for furnace applications and provides high-quality refractory material.
Refractory Application
Our quality refractory materials are widely used in furnaces, kilns, incinerators, and reactors.
Refractory Design
To minimize heat loss from the furnace, we design top-quality refractory to contain the heat generated by burning fuel.
Refractory Material Selection And Engineering
Our skilled team of engineers understands the need for furnace applications and provides high-quality refractory material.
Refractory Application
Our quality refractory materials are widely used in furnaces, kilns, incinerators, and reactors.
Refractory Patching And Maintenance
MMP refratech uses various refractory patching techniques to minimize furnace and boiler shutdown times. Major techniques involve dry gunning, wet gunning, thermal spraying, injection, casting, and patching.
Thermal Audit And Heat Loss Identification
MMP Refratech team conducts advanced thermal audits to identify accurate heat loss for best-in-class refractory maintenance.
Heat Loss Saving Coating Applications
The process MMP Refratech uses to assess the heat loss of furnaces and boilers and provide solutions ensures a reduction in shell temperature, increased refractories life, reduced fuel consumption as well as reduced downtime.
Energy Saving Calculations Before And After Application
To minimize heat loss from the furnace, we design top-quality refractory to contain the heat generated by burning fuel.
Furnace Mechanical And Electrical Maintenance
We Provide annual and customized maintenance services for the furnace, including lineup and repair for better performance.
Energy Saving Calculations Before And After Application
To minimize heat loss from the furnace, we design top-quality refractory to contain the heat generated by burning fuel.
Refractory Patching And Maintenance
MMP refratech uses various refractory patching techniques to minimize furnace and boiler shutdown times. Major techniques involve dry gunning, wet gunning, thermal spraying, injection, casting, and patching.
Thermal Audit And Heat Loss Identification
MMP Refratech team conducts advanced thermal audits to identify accurate heat loss for best-in-class refractory maintenance.
Heat Loss Saving Coating Applications
The process MMP Refratech uses to assess the heat loss of furnaces and boilers and provide solutions ensures a reduction in shell temperature, increased refractories life, reduced fuel consumption as well as reduced downtime.
Energy Saving Calculations Before And After Application
To minimize heat loss from the furnace, we design top-quality refractory to contain the heat generated by burning fuel.
Furnace Mechanical And Electrical Maintenance
We Provide annual and customized maintenance services for the furnace, including lineup and repair for better performance.
Refractory Heat-Up And Dry-Out Operations
By utilizing a controlled application of heat to a refractory lining, MMP Refratech removes water without damaging the refractory materials.